但是目前電動車的製造過程所產生的二氧化碳排放量相較於製造一台燃油汽車大約多了50%以上,這個部份也逐漸成為各個汽車廠家在製造過程中所投注的重點,亦即所謂對於製造過程 (汽車廠本身及供應商) 產生的碳足跡的關注,在這裡分成幾個面向來探討電動汽車生產過程未來如何達成零碳排......
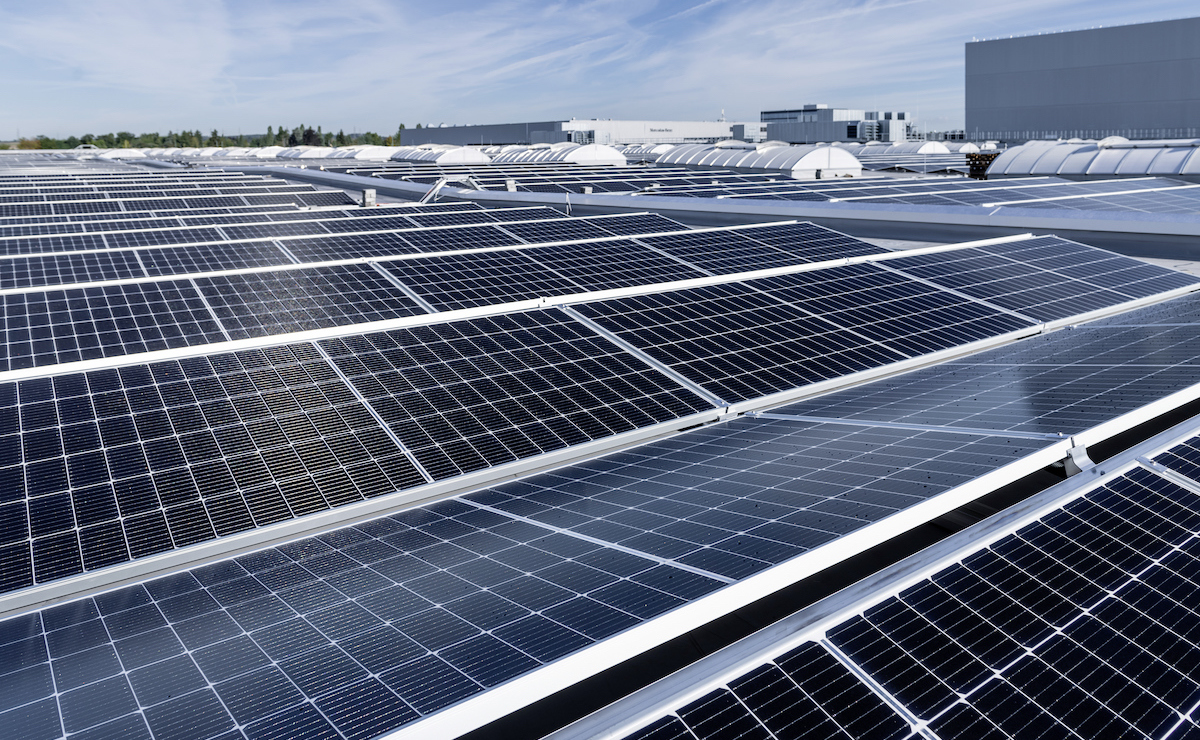
1. 風能、太陽能、水能、氫能...... 等等綠能的運用範圍,在未來幾年會有大幅改變。預計在2026年,可再生能源的發電量就會超越煤炭發電廠的發電量,在全球的ESG永續發展方案中,到了2040年,風力及太陽能將提供 40%的能源,加上水力發電‚生質能與氫能,就會超過2/3的能源是來自於零碳排方式所產生,這對於電動車製造而言也能大幅降低二氧化碳的產生。至於台灣,在國發會於今年的3月30日所發佈的台灣2050淨零排放路徑及策略總說明中也明示在2050年台灣的使用電力中,可再生能源佔比至少在70%到83%之間。由此可看見未來愈來愈多的電動車生產量因為再生能源的使用愈來愈普及,將不會造成在二氧化碳排放量的增加。
2, 製造車輛的方式,以目前傳統的汽車製造廠,從車身到塗裝一直到引擎底盤及車室組裝線,會在車輛製造過程中產生二氧化碳的地方,主要是在車身結構的焊接以及引擎變速箱底盤的組裝測試,還有車輛終檢線的靜態與動態的測試,對於電動車的生產線而言,目前僅剩下車身結構的焊接製程還會存在產生二氧化碳的疑慮,而這個製程在特斯拉於2020年新上市的Model Y的下車體製程中已經看到一些解決的方式,Model Y在加州工廠運轉了世界最大的車身壓鑄機來整合生產下車體為單一鑄件,把原本的70幾個鑄件簡化成一個,省略掉所有的焊接程序,不用投資機器人進行複雜的製造過程,當然整個下車體的安全性,行車靜肅性,車身輕量化都一步到位,也把產生廢料的可能性降到最低。從這樣的改變我們也可以看到未來的車身結構製造過程,焊接的方式將會成為一個過去式。從而也讓電動車的製造過程中的零碳排能夠實現。
3. 製造車輛的原料,目前車輛的原材料中最重要的就是鋼鐵及鋁材,目前煉鋼廠所使用的還原鐵礦石的方式,從最容易產生二氧化碳的煤炭煉鋼廠,到後來能夠有效減低碳排的天然氣煉鋼廠以至於電弧煉鋼廠,都還是會無法達成零碳排的任務,直到氫能煉鋼廠的實際運轉出現才為此項議題得到解決。瑞典的鋼鐵製造商SSAB的HYBRIT 計畫已經在去年6月成功用綠氫能源生產第一批無化石燃料的綠色鋼鐵並交付給VOLVO汽車,並於去年10月打造出首輛的綠鋼貨車,SSAB預計在2026年可以大規模商業販售綠色鋼鐵,而瑞典VOLVO汽車也宣示將在2030年達成SteelZero倡議中對於鋼鐵採購的嚴格要求,採購綠色鋼鐵來製造汽車,並於2050年達成所有鋼材皆是“乾淨、零碳”,這將可以使鋼鐵所佔的20%到35%車輛的碳足跡從此消失在車輛的生產過程之中。而製造綠色鋼鐵不只SSAB一家而已,瑞典還有一家H2 Green Steel ,乃至於日本的新日鐵,韓國的浦項鋼廠,甚至台灣的中鋼公司都有投入這項氫能煉鋼的競賽,更遑論汽車第一大國的中國鋼鐵廠家了,筆者預估2030年之後,綠色鋼鐵原材料將會是各家汽車廠商採購的首選殆無疑義。至於其他的車輛原材料比如車室內的皮革、塑料、玻璃、燈具等等也都將在此零碳排規範下一一達成目標。
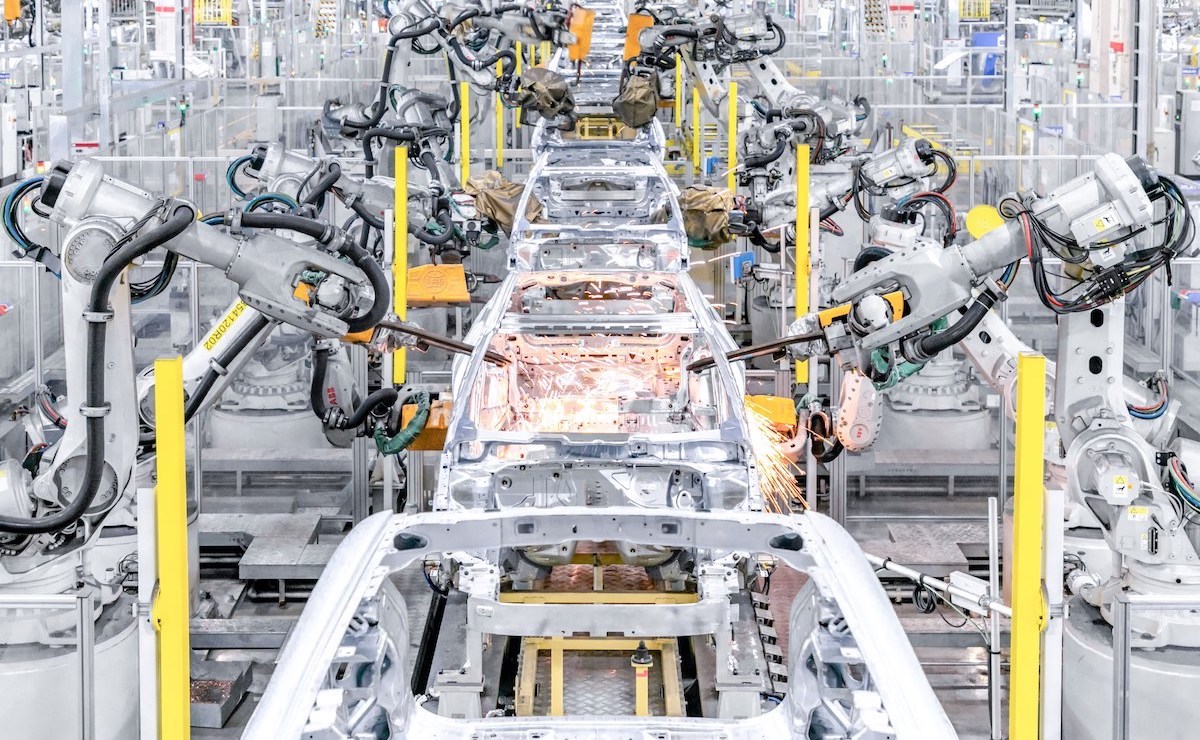
筆者最後以MERCEDES-BENZ Factory56工廠為例,BENZ在2019年就發布了名為「Ambition 2039」的計畫,最終目標是在2039年達到出廠新車零排放,零件生產過程、車輛組裝過程全面零碳排放。而這座在2020年建成的Factory 56就是以零碳排為設計概念去執行的新時代工廠,工廠位於德國的辛德爾芬根(Sindelfingen) 。整體而言,Factory 56的總能源需求比其它現有的汽車工廠低25%。而且在工廠屋頂上有裝置太陽能發電及儲能系統,為工廠提供30%電力需求。Factory 56只用一個樓層進行所有的生產流程,而且也不用任何紙張,所有生產車輛的資訊透過工廠的顯示螢幕及工作人員隨身的數位設備立即更新。Factory 56創新的裝配系統也為整個車型提供更靈活的生產可能性,這座工廠不但生產新一代S-Class短/長軸距車系以及Mercedes-Maybach S-Class 與第一款純電動車S-Class:EQS。所有的生產線支援皆由無人駕駛運輸系統負責。任何新產品及任何相關的新技術設備導入,只需更改自動導引運輸車 (AGV) 的行進路線即可。從以上的描述中我們可以窺見未來的汽車生產工廠除了利用大量的IT/5G通信系統及無人運輸載具降低能源損耗之外,彈性靈活的生產流程使得車型多樣化組裝成為可能,這在未來因應市場需求變化時更有本錢立即調整,至於自產綠色能源供給工廠的運作方式也會成為汽車工廠的標準配備,而以前習慣稱呼現場人員為藍領工人的名稱可能也要有新的名詞因應新時代了。
作者簡介-Kenny Liu 劉宸志(金豊)
1988年在成大航太系畢業,當了兩年空軍機工長之後,就在1990年7月開始進入汽車產業服務直到現在,從一開始在達亞汽車擔任服務工程師,並曾在服務廠現場擔任技師三個月,接著在羽田機械擔任Peugeot/Daihatsu產品專員,1992年3月至慶眾汽車VW T4擔任行銷及通路專員,1994年2月到台灣通用汽車(GMT)擔任地區經理,1998年9月到福特六和汽車擔任營銷及服務/零件各部門主管,2019年5月福特六和退休後自當年8月擔任JLR Taiwan經銷商營銷及服務主管及人員的專任顧問講師,並於2021年4月應聘擔任SUZUKI億和汽車公司總經理職務到2022年4月為止。