Back in January this year, Nissan signed a cooperation agreement with the Kitakyushu city government, planning to invest ¥153.3 billion (approximately NT$31.7 billion) to build a dedicated battery plant. To encourage domestic battery production, Japan’s Ministry of Economy, Trade and Industry (METI) pledged up to ¥55.7 billion (approximately NT$11.5 billion) in subsidies. However, with Nissan's business performance continuing to lag, the company reassessed and concluded that it could not bear the substantial financial burden, ultimately deciding to scrap the project. Nissan's decision illustrates that even with government support, traditional automakers still face immense financial pressure and market uncertainty in the transition to electrification. Battery manufacturing is not only capital-intensive but also technologically demanding, with rapid updates that leave little room for missteps.
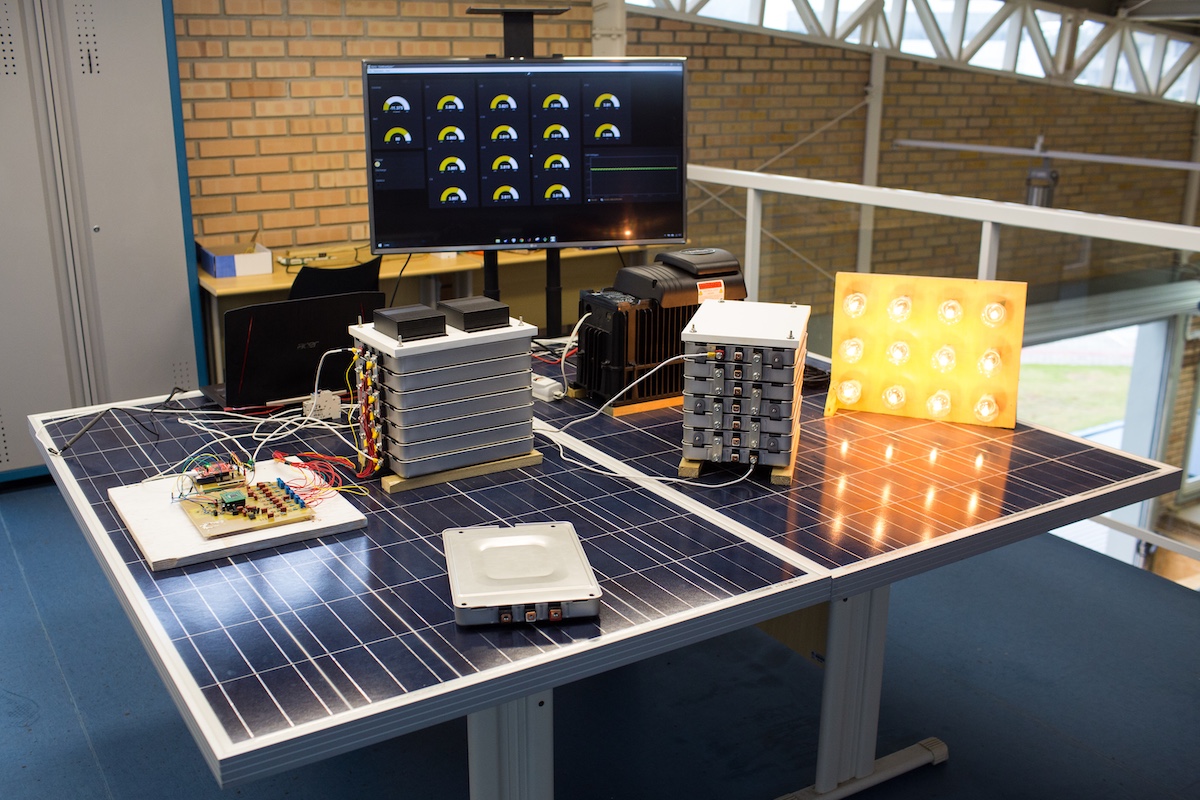
According to METI’s roadmap, Japan aims to boost its domestic battery production capacity to 150 GWh per year by 2030 to enhance supply chain independence and support local investments by automakers. So far, the government has approved around 30 subsidy projects, covering battery components and raw materials, with an initial goal of reaching 120 GWh in annual production capacity. However, the cancellation of Nissan's plant makes achieving this target even more difficult. On one hand, the loss of such a high-profile flagship investment may shake the confidence of other potential players. On the other, it underscores that even with policy incentives, the absence of a sound business model and sufficient industrial momentum can still prevent projects from being realized.
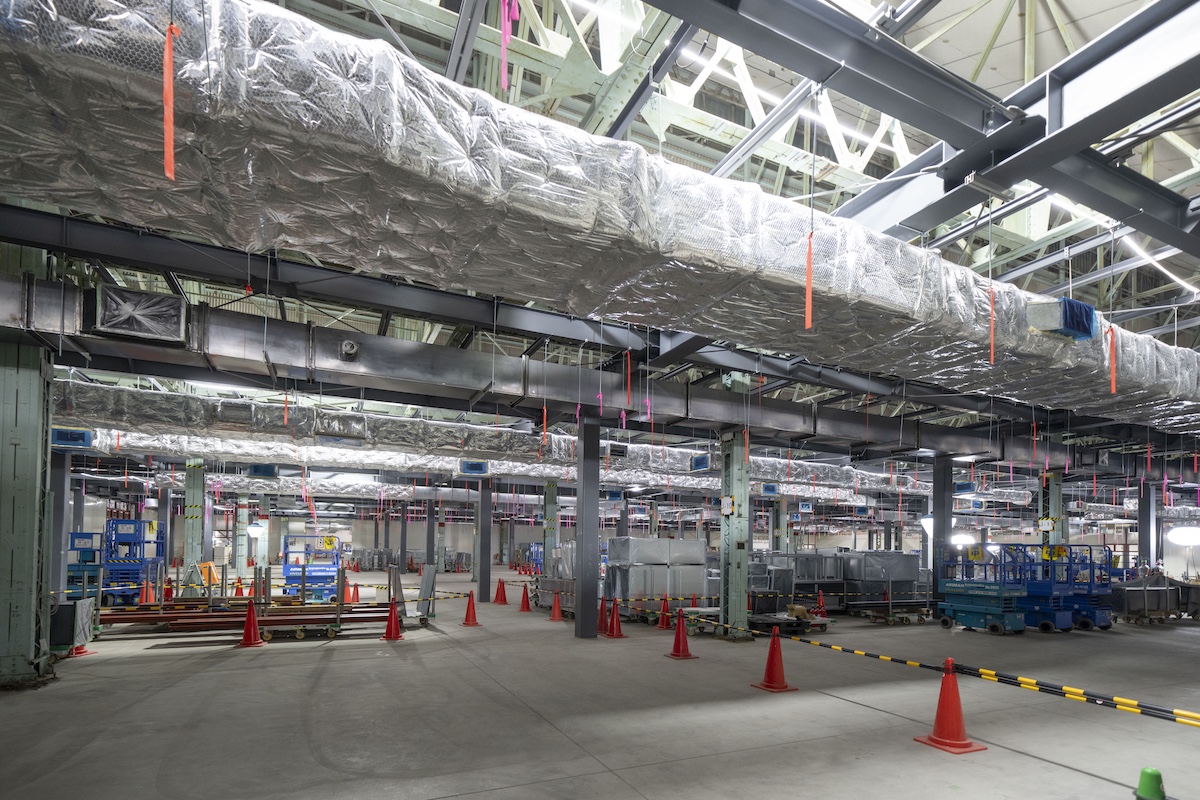
Currently, the global battery supply chain is dominated by companies from mainland China, South Korea, and Europe. China’s CATL and BYD lead the world in both technology and production capacity, while South Korea’s LG Energy Solution and SK On are aggressively expanding into U.S. and European markets. In contrast, while Japan has legacy players like Panasonic, it is clearly lagging in terms of domestic investment scale and speed.
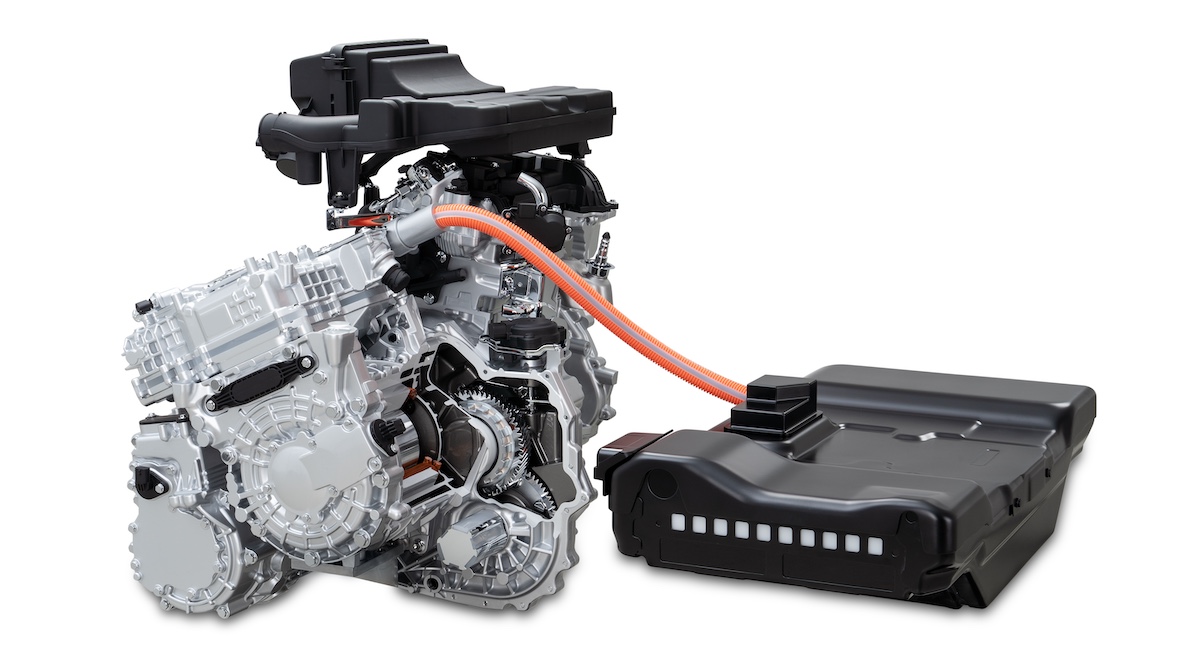
With Nissan's project falling through, concerns have grown that Japan may be falling behind in the electric vehicle era. The lack of a domestic battery supply not only increases dependence on foreign sources but may also weaken Japanese automakers’ future competitiveness in global markets. Japan has long been known for high-quality manufacturing and engineering, but whether it can adapt its strategy and investment pace in time during this EV industry transformation will be critical in determining the fate of its automotive sector.
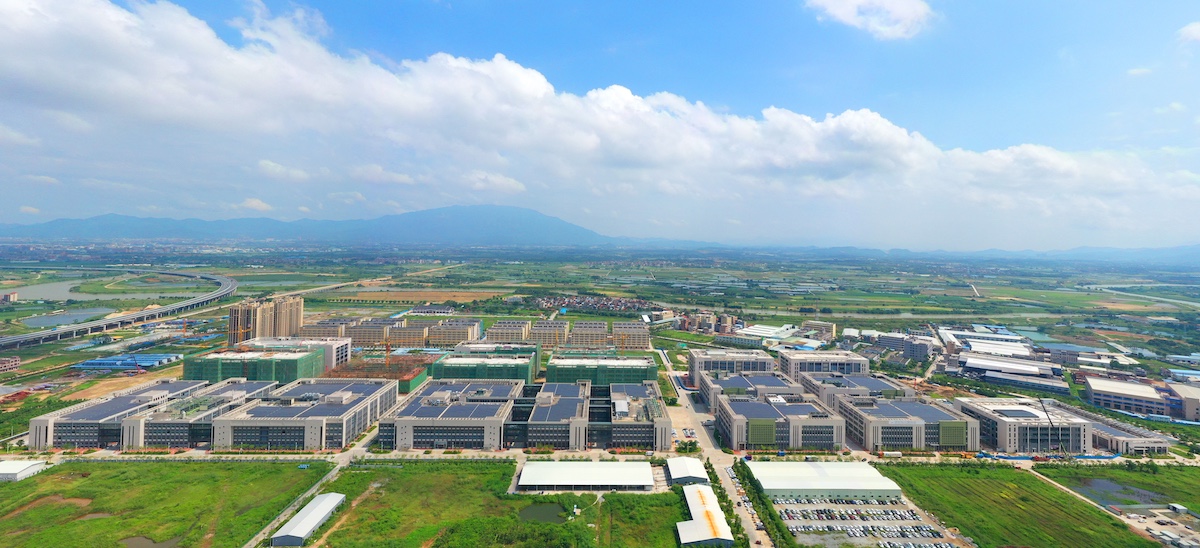