There are still lots of barriers for promoting BEVs. Aside from range anxiety, convenience of charging, and unaffordable prices, the worries are mainly about battery lifetime, this issue is also related to the residual value. The common definition of battery life is that the rechargeable capacity drops to under 70%; as batteries will lose their capacity during the charge/recharge process due to chemical effects that accumulates crystals onto electrodes, to cause the capacity loss. Carmakers usually recommend owners to keep the in-use capacity between 20% to 80%, so that the electrodes will be kept in the normal status, and the lifetime will be intact. In other words, it means that the in-use capacity should not be too low or too high. But these recommendations are too idealized, as the usable mileage will be 60% (= 80%-20%) only. So, how do we solve these problems to improve the battery lifetime?
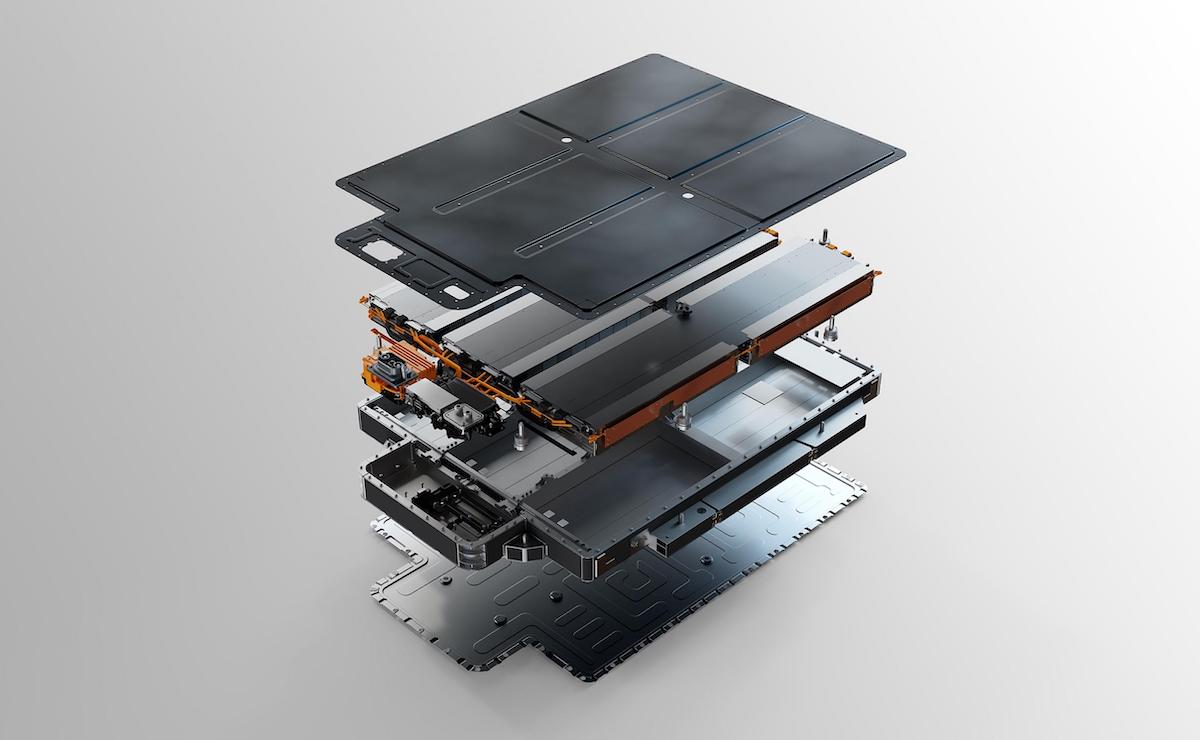
First, Let’s take a look at the combination of battery packs… battery, cooling pipe, and the management module. The most critical one is the management module among these. It’s responsible for managing the charging rate, voltage, current, and temperature control, etc. For instance, when DC high voltage charging is in progress, the charging time and other indices must operate harmoniously so as not to harm the battery. Furthermore, the lifetime is equal to the total mileage, and the factors include energy density, recharge/discharge times, and the space utilization of its outer case (related to the total capacity). In addition, safety, stability, and performance of recharge/discharge must be considered in design. There are innate technology limits of today’s lithium-ion batteries for these factors, so that it’s not east to have revolutionary breakthroughs. Despite this, R&D personnel around the world still do their best to explore and experiment from each technology perspective, to find out the solution for the next generation batteries…
1) Energy density:
- NCMA batteries. It’s based on NMC batteries but the formula has been adjusted. The ratio of nickel has been increased, then added aluminum, and the cobalt has been decreased, so that the energy density and the stability can be improved, and the cost can be reduced at the same time. But the difficulty of managing the manufacturing process will be higher.
- Lithium-sulfur batteries. The hottest topic in battery industry lately is that the lithium-sulfur batteries had finally been developed to the stage of commercialization. This low-cost battery is claimed to have three times of driving range compared with the current BEVs, but its recharge/discharge times perhaps will be reduced by half. The driving range are about 50% more with the combined effects of these two characteristics. In addition, the lightweight advantage will be preferred by carmakers.
- Full solid-slate batteries. The theoretical advantages of solid-state batteries are almost overwhelming… Because electrolytes are solid, then the most crystal-related problems have been solved, and it can have four times more recharge/discharge times comparing with the current lithium-ion batteries; and the negative electrode can be substituted by metallic lithium
by instead of graphite, so the overall weight is reduced and the energy density is improved by about 50%; the safety is relatively high due to no need for liquid electrolyte. The only disadvantage is the effective contact surface of electrodes are not as complete as liquid electrolyte, so the transmitting rate of ions will relatively reduce, which slow down the recharge/discharge speed of solid-slate batteries. It may take about 6 to 7 years for solid-batteries to be commercialized as the development is not as expected, and I believe that the actual data at the time should not be as excellent as the theoretical data mentioned above.
2)Recharge/Discharge times:
- The NMC batteries that is mainstream in the market has about 1,200 recharge/discharge times, in the same time LFP batteries has more than 2,000 times. The “Self-repair” technology of batteries emerged recently, which utilizes the add-on software and hardware of the management system to improve the lifetime of various batteries mentioned above. This technology can identify battery cells that has low performance or overheating problem during charging/discharging process, and it could stop cells from operating and to help them self-repair until they go back to normal when the vehicle is running. But how this patented new technology can repair battery cells and improve the recharge/discharge times might be still confidential, so there is no further description about it.
3)The space utilization:
- Battery packs are usually installed at the bottom of a car, and the space is limited so the utilization rate is very important, or the battery capacity will be influenced. The space utilization of traditional cylinder battery cells is about 40% because there are lots of gaps in this pattern; The LFP blade type batteries made by BYD are flat in appearance so they could be inserted into the battery pack to increase the utilization rate to 60%, which makes the energy density of the battery pack equal to NMC batteries, but have the advantages of longer lifetime and lower cost.